Early-stage implementation key to successful digital design and delivery
Authors
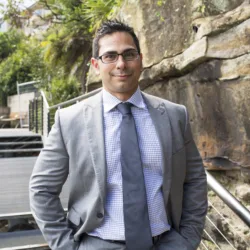
Mohammad Ali
View bioFor some years now, industry experts have been flagging the slow rate of technology adoption in the construction industry as a missed opportunity to lift everyone’s game on quality, compliance and productivity. The report released by the NSW Office of the Building Commissioner in late 2021, for example, found that 57% of builders in the Class 2 sector and 48% of designers are at what the report called a “basic stage of digitalisation”.
This means around half of the industry are missing out on benefits including improved accuracy, reduced defects and rework, more effective project team collaboration and savings on time and cost. The authors concluded it will be at least a decade before the whole industry reaches digital maturity.
That is a very concerning timeframe, because until we get there, we will struggle to achieve the goals and recommendations of other significant industry reports including the Shergold and Weir Building Confidence Report.
Shergold and Weir specifically recommended that all commercial buildings be handed over with a digital building manual that includes: as-built construction documentation; any assumptions made in developing performance solutions; building product information including details of maintenance requirements; and. Any conditions of use such as occupant numbers, loads and replacement periods for any products.
The report was released back in 2018 and we are collectively not even close to there yet, according a Federal Government report into construction industry digital-readiness released last month. There are still buildings being completed and handed over with incomplete documentation, and there are still projects being built that lose a significant share of project time and cost budget to rework and defects rectification.
Meanwhile, the NSW Government and Victorian Governments are both putting in place regulatory and administrative measures that will require specific categories of projects to implement fully-digitised project documentation.
In NSW it is the Class 2 – multi-residential buildings – currently in the spotlight, with the new Strata Hub portal requirements for digital lodgement of all design documentation including engineering designs and designs for those buildings systems most prone to defects and failures including waterproofing and fire safety systems. In Victoria, publicly-funded projects need to utilise BIM and comply with the requirements of the Digital Assets Strategy.
This might all seem quite onerous to small and medium-sized enterprises that comprise most construction industry businesses. As the OBC report found, most of them do not have the staff or the time to upskill in digital approaches to design, project management and project documentation.
That’s where taking an integrated design approach can build subtrade capacity in utilising digital approaches while also achieving significant cost and time savings for contractors and reducing the risk of defects and rework. Also, these approaches can deliver the kind of significant building performance improvements across energy-efficiency and thermal comfort that mean an asset will still be relevant a decade from now when expectations for net zero energy become normalised in the property sector.
Forget 2050 – all indicators are that by 2030 any asset that is not at or near net-zero for carbon emissions will be very hard to sell, rent or insure.So, there’s both a short-term gain and a long-term benefit to putting more digital smarts into projects at the earliest stages and using those platforms to bring the entire project team together and coordinate all documentation for the entire project lifecycle.It’s never been easier to achieve. Integrated design used to require getting everyone in the same room regularly or passing around a mountain of paperwork that needed to be compiled, filed and otherwise made manageable.
This is part of the reason early team integration was not standard practice on many business-as-usual commercial lump sum or D&C projects.
What might have been thought of as time and cost savings achieved at the front end by reducing consultant and design team hours in meetings and discussions, however, often turned into delivery team hours and additional costs from rework caused by defects and clashes. It also potentially passed risk and cost along to the buyer in terms of suboptimal energy efficiency outcomes and corresponding high energy costs.
Integrated design and lifecycle thinking is the best way to deliver a building. For example, an integrated design approach applied at Sydney Airport T1’s refurbishment of 31 departure lounge gates enabled us to achieve design accuracy and resolve all design coordination issues prior to reaching site. That meant the contractor could provide cost certainty to the client about the project as well as deliver to the project to the client's expectations. We were also able to complete life cycle assessment and determine the best outcomes to improve the passenger experience while minimising energy consumption.
With Marrickville Metro shopping centre development, the client's goal was to have an industrial-looking shopping centre to celebrate the heritage of the suburb and engage with it. With an industrial look and feel, the key focus will be the services having an exposed ceiling. The building services being digitally designed enabled the team to visually understand how the building services interacted with the space and design with that in mind.
It gave the design team the chance to visualise what would happen and then enabled the contractors to understand the client’s vision and intent and deliver it to that expectation and also provide price accuracy for the client when tendering. We also managed to coordinate all the services to not only be aesthetically appealing but also model them to be efficiently laid out, and model the natural ventilation on the ground floor plane of the retail centre to allow the ventilation to work effectively and improve the overall operational energy efficiency.
Similarly, when designing a data centre, energy-efficiency is crucial as data centres are under the microscope for their energy use. To optimise efficiency, every part of the whole is considered not only individually, but in relation to everything else. Building envelope, building orientation, electrical systems, security, hydraulics, fire safety and HVAC are all designed as part of a whole package.
What makes this possible is having a digital engineering design approach that is integrated with digital project management, digitised communications coordination, digital everything. This is not an added line item – it actually delivers efficiencies in time and cost.
Using a digital design approach means programme can be more effectively developed, clashes and potential pinch points can be foreseen and dealt with at the program design stage – before everyone is on-site. Done right, it also lays the foundation for the contractor to integrate the information that will enable the development of a digital twin for the final asset.
Even a project that does not proceed to full digital twin stage but has digitised project documentation, a tagging strategy, smart controls on building systems and product and system specifications will be more efficient to operate and maintain – and ideally more comfortable to occupy.
Reports on the extent of digitalisation and quality of construction aside, there is still significant work needs doing to convince many of those commissioning buildings to understand the value proposition. Clients need to understand the value of allocating budget to the early design stage, and the capability of digital approaches to give them a more future-fit and operationally efficient asset at handover should be the clincher.
This article was originally published by Sourceable on May 12, 2022